Fashion’s favorite materials have a steep environmental cost.
Polyester leisurewear is stretchy and comfortable, but its threads are spun from petroleum, shed environmentally-harmful microplastics when washed and barely biodegrade, losing just 1% of mass after 660 days in a landfill, according to a 2021 study in the journal SN Applied Sciences. The ubiquitous cotton T-shirt requires 6,000 liters of water to be produced, according to the World Wildlife Fund, which is the equivalent to what a person drinks in 900 days. Using up this scarce resource also contributes to soil erosion, according to a 2020 United Nations report.
Leather production relies on raising livestock, an industry that was responsible for cutting down 45.1 million hectares of forest between 2001 and 2015, according to the World Resources Institute.
In an attempt to turn the tide, researchers, companies, and brands are dreaming up technological solutions: innovative fabrics that imitate the characteristics of fashion’s traditional raw materials, but without the environmental damage.
Plastics from nature
Fossil-fuel-derived materials make up the majority of fabric used in clothing — about 65 percent in 2021, according to a report by the global nonprofit Textile Exchange, which works to help brands and companies identify and adopt materials that are better for the environment and human and animal welfare. In order to end the industry’s dependence on fossil fuels, scientists are trying to develop alternatives to fabrics such as polyester, nylon and spandex that behave in similar ways but come from renewable sources, unlike petroleum. With clever chemistry, scientists can turn plant-based oils or starches into the components of plastics.
Most consumers are already familiar with bio-based plastics in the form of compostable plastic food packaging or dinnerware derived from fermenting starches such as corn. These products are made from polylactic acid, and do biodegrade but only in industrial composting conditions. For example, a May 2023 study found that textiles made from PLA did not show signs of degradation when hung off a pier into the ocean in Southern California for a year, making them still a concern for ocean pollution. In 2023, San Diego-based biotech company Genomatica announced a collaboration with Lululemon on two shirts made from nylon-6, which is derived from sugarcane and corn and can be recyclable, depending on how clothes with it are produced, the company told Vogue Business.
But nylon only represents about 6% of textiles, according to the aforementioned Textile Exchange report, and replacing polyester, which represents 54% of all textiles, has presented a greater challenge. The most common polyester used in textiles is made up of two molecules, polyethylene and terephthalic acid, which is why it’s referred to as PET. Polyethylene, an alcohol, is relatively easy to replace with a plant-based source. Examples include 37% corn-based Sorona fabric by CovationBio, a company which began as a part of chemicals giant DuPont, and Ecodear thread by Toray, in which the polyethylene comes from sugarcane. Both use petroleum-based terephthalic acid. California-based Origin Materials, which calls itself a “carbon negative materials company,” said they have developed a way to derive both molecules from wood residues; they’re in the process of constructing their first plant and have already signed on LVMH, and in the food industry, PepsiCo.
“I think there’s plenty of opportunity to find drop-in replacements,” said Mike Burkart, a professor of chemistry at the University of California, San Diego, referring to plant-based plastics that can be seamlessly exchanged for existing materials in factories and production lines. Burkart and his colleagues have developed a form of biodegradable polyurethane made purely from microscopic algae. Their startup company, Algenesis Materials, has launched its own shoe brand and plans to release a flip-flop in partnership with surf-sandal brand Reef.
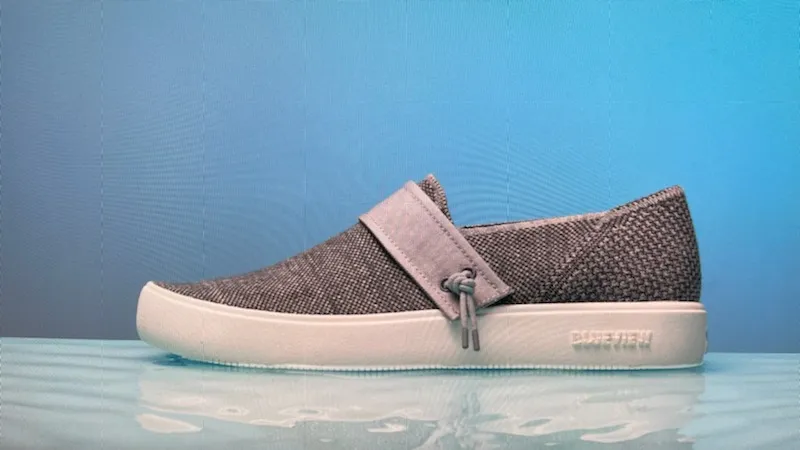
Unlike PLAs, Burkart said, Algenesis’s algae-based polyurethane degrades within six months in a backyard compost or in one year if it’s tossed into the ocean. As the experiment with PLAs illustrates, a bio-based polymer isn’t necessarily easily biodegradable. However, Burkart said the properties of polymers can be altered. It’s just a matter of decoding the chemistry.
“When I got started in this research I was worried that maybe I wasn’t going to find anything interesting because polyurethanes are a 100-year-old technology,” Burkart said. “But it turns out there are all kinds of things because the science has just kind of skipped over it.” Plastic engineers wanted to “make materials that could last forever, and they succeeded,” he explained, while engineering a plastic to biodegrade “is a chemistry that had been ignored and avoided.” Until now.
Weighing environmental effects
Ideally, the industry will use a plant-based PET that can be recycled in the way pure petroleum-based PET can be recycled, said Sonja Salmon, a professor of textile engineering, chemistry and science at North Carolina State University in Raleigh. Salmon, who authored the 2021 study on textile biodegradability, said recycling other types of plastics is not so straightforward because of their chemical composition; cotton-polyester blends are also not recyclable. Currently the focus has been on melting down used plastic and spinning it into clothes — think water bottles into clothes. To achieve true circularity, producers would want to chemically recycle textile polyester — a process that is still too costly to compete commercially, she said, and research is underway to bring the costs down.
Plastic engineers wanted to “make materials that could last forever, and they succeeded.”

Mike Burkart
professor of chemistry at the University of California, San Diego
Additionally, a bioplastic can’t be assumed to be better for the environment just because it’s not derived from petroleum. Weighing the environmental impact requires a scientific life cycle assessment. For example, as cultivation of a certain raw material of bioplastic — what’s called a feedstock — scales up to meet industrial demand, it could have unforeseen impacts on water, habitats, and food security. Origin Materials said their wood is sourced from sustainably-farmed forests and that they can use waste wood and even cardboard. Burkart touted the fact that algae, such as his company's, is grown using brackish water in large tanks that can be installed on land that isn’t arable. According to a 2013 paper by the independent Nova Institute, which offers consulting on renewable materials, corn or sugar-beet-based plastics take much-needed arable land away from the cultivation of food crops. However, the same paper noted that corn raised as feedstock for plastics could be used as food in the case of a global shortage.
For bio-based plastics to be widely adopted, Burkart said, there needs to be pressure on companies to switch from government regulation. If the incentives are there, “we could replace these things within the next ten to twenty years,” Burkart said. “I firmly believe this is possible.”
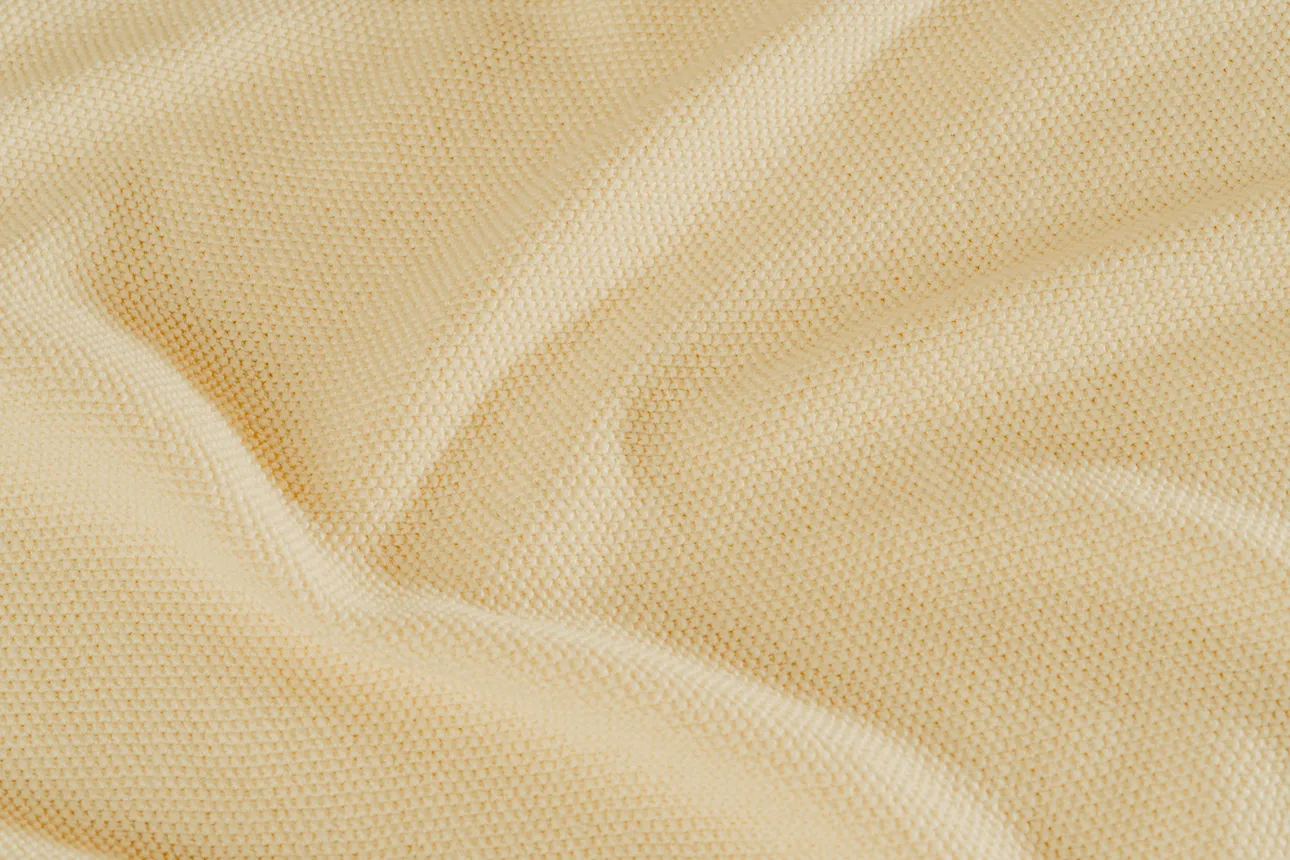
Finding cotton alternatives
The other main fabric in use, cotton, accounted for 24 percent of the global fiber market in 2021, according to the same Textile Exchange report.
“Cotton is a beautiful fiber, I mean, nature gave us a gift,” Salmon said. “It is a highly engineered fiber, a single cotton fiber is one single plant cell, and the way nature has assembled that single plant fiber and allows us to spin it into fabric is amazing.” Nevertheless, she said, there’s a strong motivation to look for alternatives because of its impacts on water and land. According to the aforementioned 2020 United Nations report, cotton, despite using only 2.5% of the earth’s arable land, accounts for 16% and 4% of the world’s use of pesticides and fertilizers respectively — and those toxic chemicals leach into the ecosystem where cotton is grown.
Although hemp has long been a less environmentally-taxing alternative to cotton — as long as it isn’t grown or processed with chemicals — new fibers are emerging from unexpected sources. Some involve replacing some or all of the cotton in a fabric with another plant. For example, Life Materials’ Weganool blends 70 percent cotton with calotropis, a weed that doesn’t need fertilizer, water, or pesticides. Flocus makes fabric from the fluffy pods that are harvested from the kapok tree, which doesn’t require fertilizers or irrigation and can be grown in polycultures. Kelsun is a cotton-like material made from 75 percent kelp and 25 percent a proprietary blend of other natural fibers. “Our initial developments have focused specifically on dropping in Kelsun in place of cotton,” a spokesperson said in a written statement provided to Fashion Dive. They hope to optimize the fabric’s biodegradability.
Similar to the case of bio-based plastics, the sustainability of these materials is in the details of how the plant fibers are cultivated and processed. This is exemplified in the way that some companies have offered alternatives to cotton by turning to an existing technology, viscose. Viscose comes from wood pulps but raises concerns because of the source wood and the toxic chemicals used to dissolve it. Tencel, a viscose developed by Lenzing, uses renewable wood and claims to have solved the solvent problem with a “unique closed loop system which recovers and reuses the solvents used,” according to the company website. Lenzing achieved a carbon neutral fabric in Sept. 2020 and has ongoing collaborations with H&M and Levi’s. Other alternatives include Italian brand Orange Fiber, which combines the leftovers of orange juice production with Tencel, and Crabyon, which uses both wood and waste crab from the food industry. Legna, a wood pulp-based fabric from the Swiss brand Muntagnard, also comes from sustainable forests and counts on an innovative recipe of non-toxic solvents that can be reused.
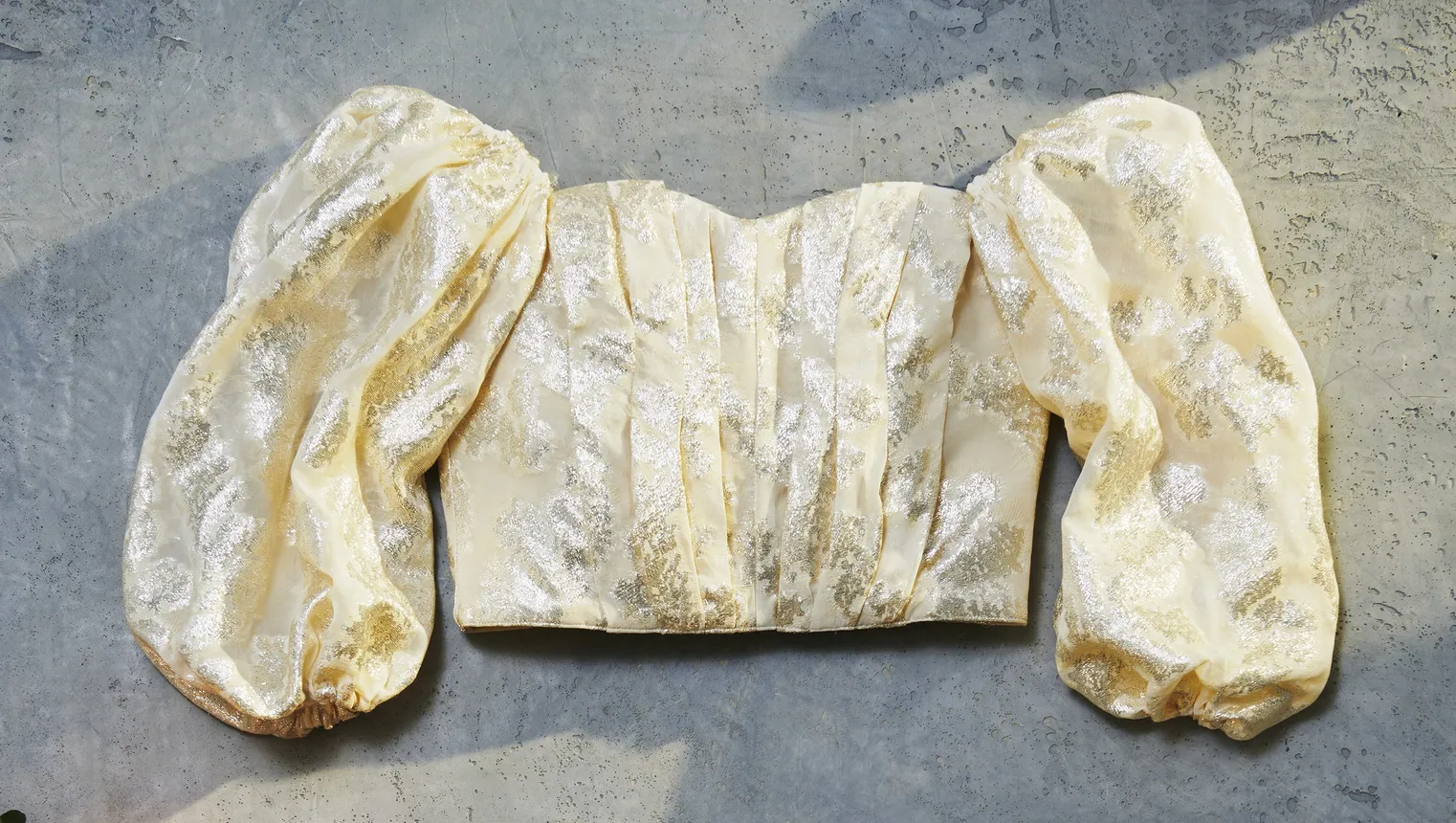
Plant-based fabrics should be encouraged, Salmon said. “Any plant that we can grow sustainably is going to help us pull carbon dioxide out of the atmosphere, which is really important.” And for that to be possible, more attention needs to go to making agricultural practices more sustainable and beneficial for the soil, and in helping the plants we depend on adapt to the inevitable consequences of climate change. “That fundamental need to improve the way we care for our soil is really important to the bio-based economy,” she said. “For the polyester to come from trees, the trees need good soil.”
“Any plant that we can grow sustainably is going to help us pull carbon dioxide out of the atmosphere, which is really important.”

Sonja Salmon
Sonja Salmon, a professor of textile engineering, chemistry and science at North Carolina State University in Raleigh
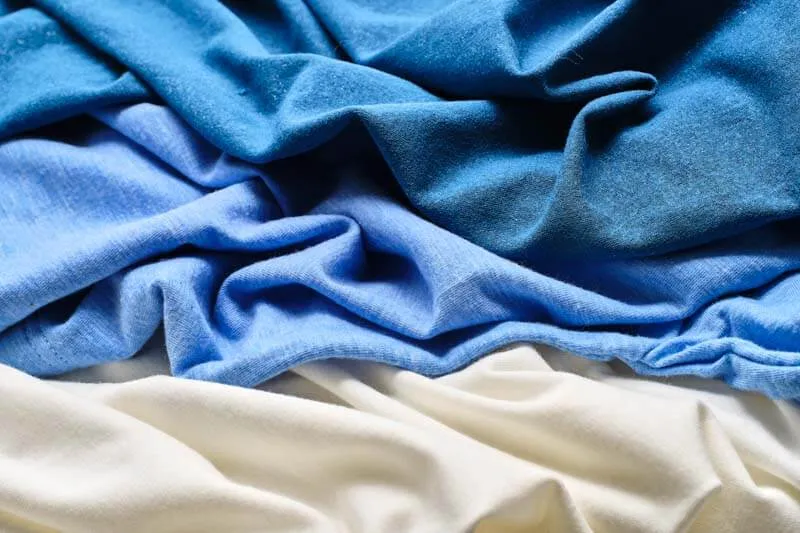
Leather without the cow
Another material that has inspired a flurry of technological innovation is leather. Raising animals contributes to deforestation: the World Resources Institute estimates that cutting down trees to make room for pasture accounts for 36 percent of agriculture-caused deforestation worldwide. Meanwhile, the tanning process involves toxic chemicals including chromium, a carcinogen. While their disposal is regulated and controlled in some countries, in others, unsafe quantities are released directly into the environment. For example, a 2022 study found that in tanneries in Bangladesh, leather shavings, which are dumped onto the land, contained concentrations of chromium of 13832.70 milligrams per kilogram, whereas the highest existing legal limit is 100 mg per kilogram, the authors say.
Some leather alternatives do double duty because they rely on food or agricultural waste in the process rather than virgin materials. Bacteria and fungi feeding on waste — anything from discarded temple flowers in India to coffee pulp — can grow into a flat mass that can be processed and made into purses. The cellulose in plant waste can be coaxed into a leather-like material: in 2020, Tommy Hilfiger released a shoe made from 24 percent leftover apple cores and peels, while discarded pineapple leaves are the raw material for Pinatex, which has been used by brands like Hugo Boss and H&M, according to the company website. Desserto, which makes their material from cactus leaves, touts their renewable harvesting process and the carbon-capturing benefits of cactus farms.
Another crop of companies have focused on mycelium, the delicate root-like structure that nourishes mushrooms. Mushroom biofiber firm MycoWorks grows mycelium into a raw material that can be processed with different finishes and colors, and last month released three new finishes for its products. The company also announced it would begin producing these materials at a commercial-scale factory in South Carolina. In 2021, MycoWorks said they would be releasing a bag with Hermès, which they say is still in production.
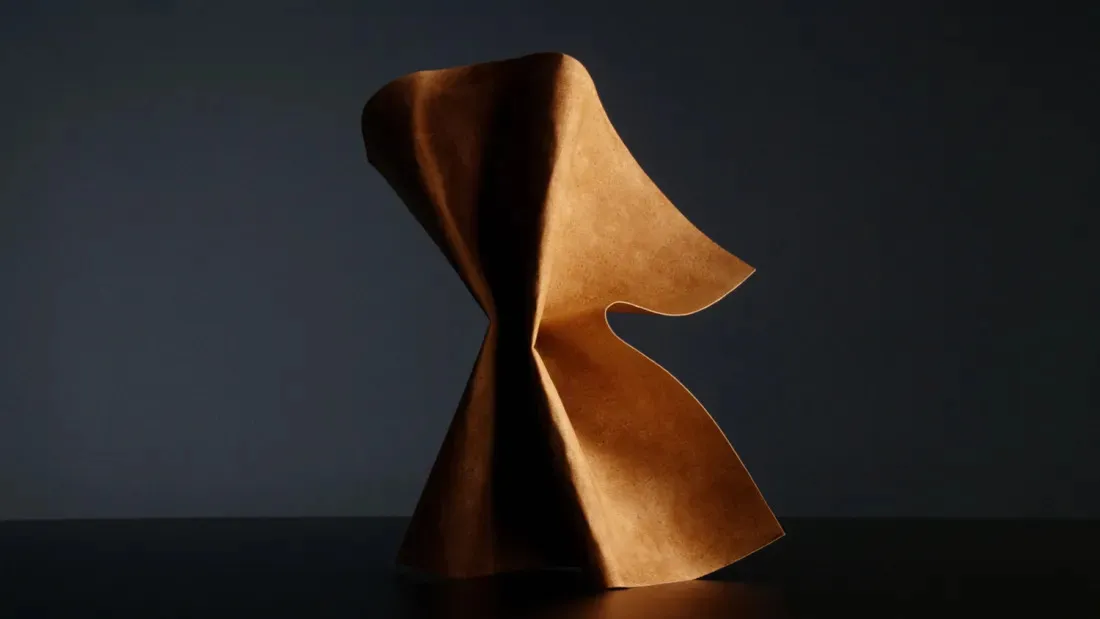
Meanwhile, textile fiber company Bolt Threads was forced to pause operations earlier this year on its leather alternative material, called Mylo, after it failed to raise enough funds to continue. The technology had been used by fashion companies including Lululemon and Stella McCartney.
Some approaches more closely resemble synthetic leather, but with bio-based components. In 2022, Everlane released a bag made from Modern Meadow’s Biotex, which combines a plant-based polymer coating with Lenzing’s viscose to achieve, the company claims, 90 percent less greenhouse gas emissions in its production than traditional leather. Natural Fiber Welding’s Mirum is based on natural rubber, plant-based oil, and a variety of plant materials, like rice hulls and coconut fibers, depending on the specifications required. “My dogs haven’t shown any interest in it,” jokes Salmon about a sample she recently ordered. “It’s not quite as soft and supple as that feel that you might get from a well-worn leather, it’s a little more vinyl-y in its texture but it’s not vinyl-based.”
Materials marketed as alternatives to leather may abound, but they vary in how they fulfill properties customers expect from leather, such as flexibility, strength, and breathability, said Michael Meyer, CEO and scientific director of FILK Freiberg Institute in Germany, an independent materials testing facility. In a 2021 study, Meyer and his colleagues tested the properties of a range of new materials, from Piñatex (the material from pineapple leaves), to a kombucha-based material (grown from bacteria and yeast), Muskin (made from fungus) and several others. Piñatex, for example, performed well on tests of flexibility, which is important for making shoes, but wasn’t as breathable as leather because of its coating, although Meyer said that making the coating thinner might resolve the issue. Muskin, on the other hand, was the weakest material but was very breathable. He also found that one vegan imitation leather, Noani, had a thin middle layer of leather fiber material.
“Up to now, nothing in the complete set of parameters is coming very close,” Meyer said. He gave the example of Piñatex; in its natural form it resembles a paper and depends on a coating to give it leather-like qualities. As for scalability, “if you’re talking about fungi, bacteria, or kombucha, it’s scalable because it’s a biotechnological process.” As of now, he said, cellulose cannot be chemically treated to get the same properties of drapability, and comfort of tanned leather. “You have a completely different behavior or chemical composition,” he said.
If the question is how to copy the structure of animal skin without the animal, another company, Vitrolabs, claims to have the answer. The company, which counts amog its investors Leonardo di Caprio and Kering, starts with cells taken from cows and claims to grow hide in the lab within weeks. But Meyer remained skeptical that a true hide can be grown with such technology and at a low-enough price, citing the still-high prices of lab-grown meat.
The cost of cultured animal products is expected to go down though, at least according to proponents of the technology. For example, a 2023 study in Nature Food by the founders of a company that cultures chicken breasts projected that, if scaled up to industrial levels, their technique could produce chicken breasts for about $4-10 per kilogram, making it competitive with the farmed version.
Are clever solutions enough?
Technological innovations in fabrics alone will not transform fashion from an environmental threat into a friend. For example, according to the 2020 United Nations report, fiber production only accounts for 12% to15% of a garment’s climate impact. To make a meaningful change, the industry will need to produce less and customers will need to quit their habit of overconsumption, fashion researchers say.
Nevertheless, a revolution is under way. The 2022 Textile Exchange report highlighted another new trend in companies trying to bypass plants altogether, capture carbon directly and turn it into polyester, with Fairbricks and Rubi being just two examples. Werewool, for instance, uses gene editing to design microorganisms that create fibers in specific colors that can be mixed with other fibers, thus avoiding the often-polluting dyeing process.
“It’s like a reawakening of the possibilities in the textile fiber industry,” Salmon said. “I think it’s a very exciting time.”